Tracing Our Past - The History and Evolution of Magnetic Particle Inspection
Introduction
Non-destructive testing techniques have evolved tremendously over the last century, and Magnetic Particle Inspection (MPI) is no exception. With origins stretching back to the 19th century, MPI has developed into a highly refined method critical for ensuring material integrity. Join us on a journey through the history of MPI to understand how it became a staple in quality and safety assurance in modern industries.
Early Beginnings
In the late 1800s, early practitioners began exploring magnetism as a tool for detecting defects in metals. One of the notable early applications was the inspection of cannon barrels, where inconsistencies in magnetic fields hinted at potential weaknesses. By 1868, the concept of using magnetic properties to assess material integrity was forming the basis for future testing methods.
Significant Advancements in the Early 20th Century
The 1920s marked a transformative period in the evolution of MPI. William Hoke made significant contributions by noticing that fine metallic particles generated during machining would reveal cracks and other defects when aligned along discontinuities in the material. This discovery paved the way for the development of more specialised MPI techniques, making it possible to visibly highlight and evaluate flaws that were previously hidden.
Development and Standardisation
During the 1930s, MPI began replacing older non-destructive testing methods, such as the oil and whiting process. The improved efficiency and reliability of MPI quickly made it a preferred choice, especially in sectors where quick and accurate results were imperative. Over the decades that followed, MPI techniques were refined further. Different magnetization methods—direct, indirect, and even the use of specialised magnetic yokes—were developed to suit a diverse array of industrial applications. The establishment of international standards like ISO 9934 and ASTM E1444 provided a uniform framework, ensuring consistent application and accuracy in MPI processes across the globe, including Australia.
Modern MPI Practices
Today, MPI is a well-orchestrated process involving meticulous pre-cleaning, controlled magnetization, careful application of magnetic particles, and rigorous post-processing. Each step has been perfected over decades of research and industrial application, ensuring that even the smallest defect is identified reliably. With innovations such as fluorescent particles that glow under UV light, the modern MPI process not only remains effective but also continues to evolve, meeting the extremely high demands of today’s safety and quality standards.
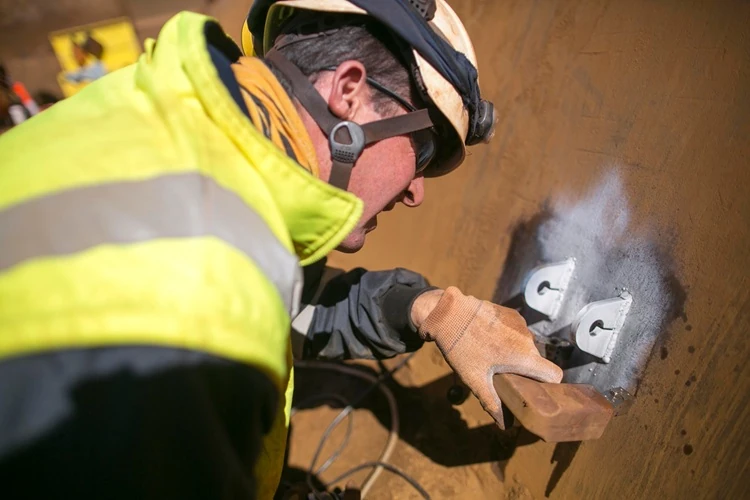
Legacy and Future Innovation
The rich history behind MPI is a testament to continuous innovation in non-destructive testing. From its inception in inspecting artillery to its current role in high-tech industries such as aerospace, automotive, and infrastructure, MPI has proven indispensable. As Australian industries continue to push the boundaries of technology and engineering, MPI is set to evolve further with advancements in digital imaging and automation, ensuring that the safety and quality standards of tomorrow are built on a strong foundation of proven reliability.
Conclusion
The evolution of Magnetic Particle Inspection reflects our enduring commitment to quality, safety, and technological advancement. Its journey from early magnetic experiments to a modern, standardised method of non-destructive testing highlights both the ingenuity of early researchers and the dynamic nature of industrial progress. Today, as MPI continues to safeguard products and processes across Australian industries, its history remains a powerful reminder of the innovation that underpins modern engineering excellence.